サステナブル工具の潮流|再研磨・再生材質
カテゴリーblog
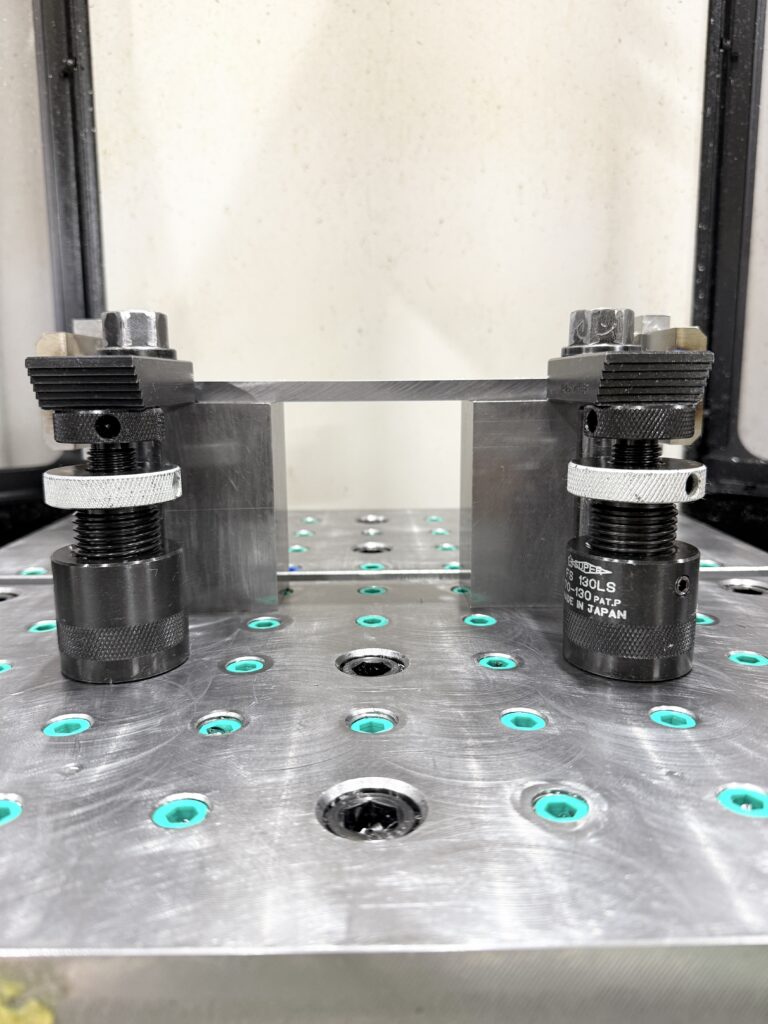
1. なぜ今、工具の再研磨・再生が注目されるのか?
- 資源制約と環境負荷への危機感
超硬合金の主成分であるタングステンはレアメタルであり、使用済工具から回収し再利用することでエネルギー消費70%、CO₂排出60%の削減効果がある 。
さらに、再生材で製品を作るとエネルギー使用は‑70%、CO₂排出は‑40%の削減が報告されており 、これはサステナビリティ視点で非常に強いインパクトです。 - SDGs「責任ある生産と消費」(目標12)への貢献
廃棄物を減らし使い道のある資源を最大限活用する取り組みとして、再研磨やリサイクルは典型的な行動例です 。
2. 国内企業の取り組み事例
① オーエスジー(OSG)グループ
- 超硬・ハイス工具を再研磨・再コーティングし、性能を新品と同等に再現 。
- 使用済超硬工具のレアメタル(タングステンなど)リサイクルにも展開 。
② グリーンツール(岡山)
- ツール全面再生・リサイクルを目指してSDGs推進 。
- 太陽光発電・EV導入など、省エネや地域貢献にも幅広く取り組み。
③ その他リーディング企業
- 青山製作所(OSGグループ):他社工具も対応、高精度再研磨+再コーティング実績 。
- 石川工具研磨製作所(1983年創業):CNC研削盤による大量対応&高品質再研磨 。
- ウンノ研磨工業所(品川):職人技による高精度刃先復活/多様な素材対応 。
- 宮本製作所(再研磨.com):多材質・多形状工具への再研磨対応、低コスト・短納期 。
3. リサイクル素材活用の展開
- 超硬合金(タングステン)回収による素材再生
住友電工は国内販売分の超硬工具をほぼ100%リサイクル 。BMWも独自で回収→粉末再生→工具製造のループ構築、年間でタングステン消費7 tを削減しCO₂を60%削減 。
サンドビック公開データによれば、再生素材使用で70%のエネルギー削減・40%のCO₂削減 。 - 工具設計における素材の効率還元
Nine9の例では、インサート形状設計で超硬使用量を95%以上削減する例もある 。
4. 市場動向と将来展望
- 市場成長率は年約14.5%予測(2025‑2032年) 。自動化・IoT・スマート保全が拡大する製造現場で、工具再生ビジネスの需要が拡大中。
- 導入メリットの定量的効果
ある精密機器メーカーでは、再研磨導入で工具費が年間320万円削減、寿命30%延長、加工精度15%向上という成果 。
5. サステナブルな工具利活用のポイント
- 技術力を内製/外注で整える:企業規模によって「内製」か「専門外注」か選択。精度・納期・コストを比較考量。
- パフォーマンス設計の見直し:再研磨ツールは新品と同条件ではなく、再研磨仕様に最適化した条件設定が不可欠 。
3. ライフサイクルとコストの見える化:複数回使用による費用対効果と環境負荷低減のスイートスポットを把握(LCA視点) 。 - ツール回収とリサイクル体制の構築:使用後の工具を回収ルートに乗せ、素材レベルで循環する体制構築が鍵。
6. まとめ(今後の展望)
- 工具の再研磨・再生は、「コスト削減 × 資源循環 × CO₂削減」の三重効果を実現する注目アプローチ。
- 市場は今後も拡大し、自動化・デジタル化による効率化と共に、サステナビリティへの投資効果も問われる。
- 大企業・中小ともに「設計・加工・回収・リサイクル」にわたる共通フレームワーク整備と、LCAに基づく最適化が求められる。