微小径ドリル切削のキーポイント|折損防止と高精度を両立するために
カテゴリーblog
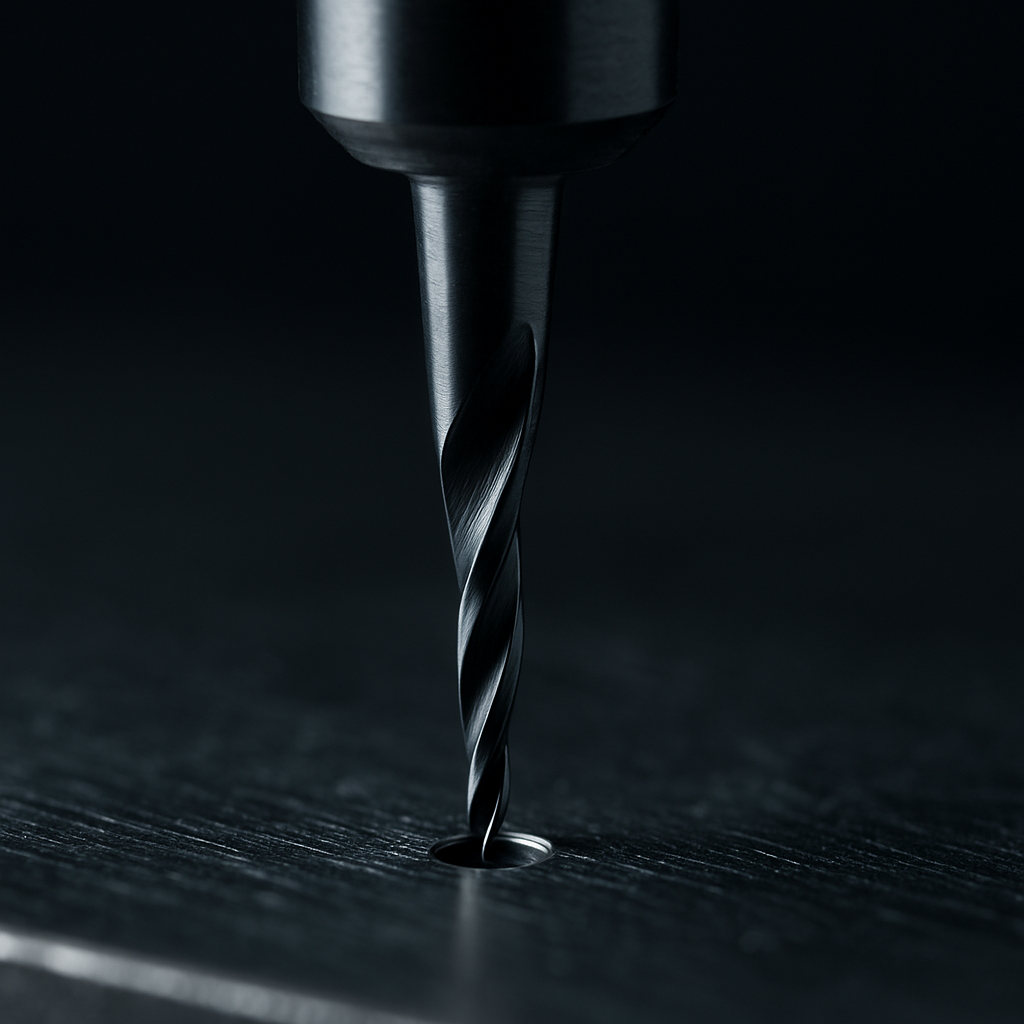
はじめに
電子部品、医療機器、精密金型などの加工では、「微小径ドリル(φ0.1~φ3.0mm程度)」による穴あけが不可欠です。しかしこの加工は、ドリルの折損や芯ずれ、切りくず詰まりといったリスクが高く、熟練者でも油断できません。本記事では、微小径ドリル加工における安定加工のためのキーポイントを解説します。
加工成功のためのキーポイント
1.
高精度チャックの使用
芯振れを最小限に抑えるため、コレットチャック(0.003mm以下)やエアチャック式を使用。
2.
段階的なセンタリング加工
先にセンタードリルで下穴を開けることで、ドリルがぶれるのを防止。
3.
切削条件の最適化
- 回転数:高回転(10,000~50,000min⁻¹)推奨
- 送り速度:ドリル径に応じて極めて小さく設定(例:0.01~0.05mm/rev)
- クーラント:内部給油 or ミスト冷却を推奨
4.
工具材質とコートの選定
- 超微粒子超硬+TiAlNやDLCコートが主流
- 耐摩耗性・潤滑性の高い皮膜で熱集中を回避
5.
Z軸送り制御と監視機能
- 加工中のドリル負荷をモニタリングし、トルク異常で停止するシステムを導入
- サイクル途中のチップ排出動作(ピーニング加工)も有効
現場での工夫例
- バキューム除去+スルークーラント併用による切粉除去対策
- 試験加工→穴径ばらつき確認→本加工の流れを標準化
- 高精度ドリルのロット管理と寿命トラッキング
まとめ
微小径ドリルの加工は**「工具精度」「加工条件」「制御精度」の三本柱がすべてそろって初めて安定します。特に折損は一瞬の振動や負荷変動**でも起こるため、事前準備とリアルタイム監視の両立が重要です。精密加工を支えるこの分野で、ぜひ自社の加工力を高めてください。
このブログを書いた人
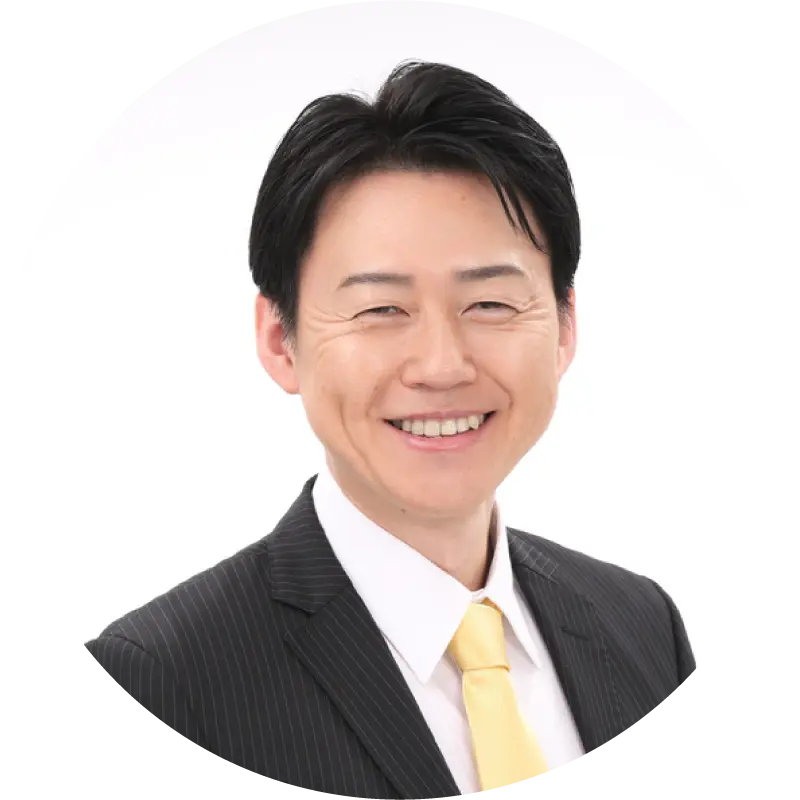
有限会社 長谷川加⼯所
代表取締役
長谷川 一英
HASEGAWA KAZUHIDE
切削加⼯の長谷川加⼯所について
切削加⼯で難しい産業部品を柔軟に製作。
アルミ・スレンレス・鉄 etc。
試作・⼩ロット量産。
詳しくはこちら
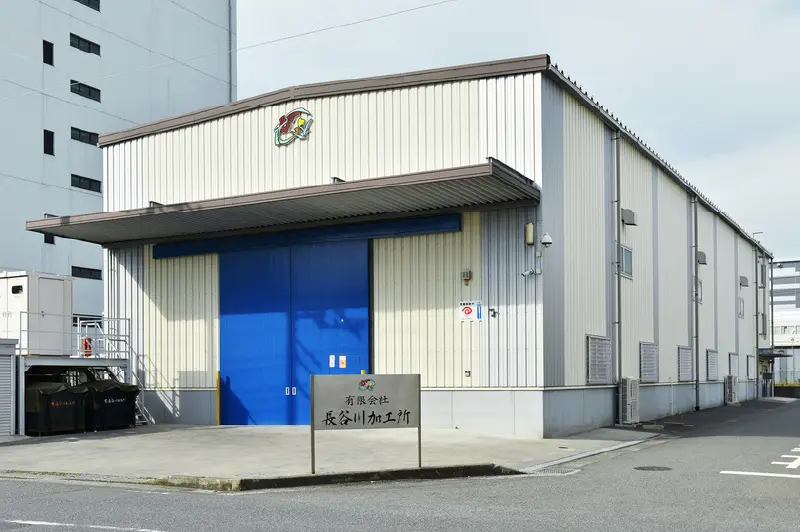