切削条件の変更で起こる工具損傷トラブル
カテゴリーblog
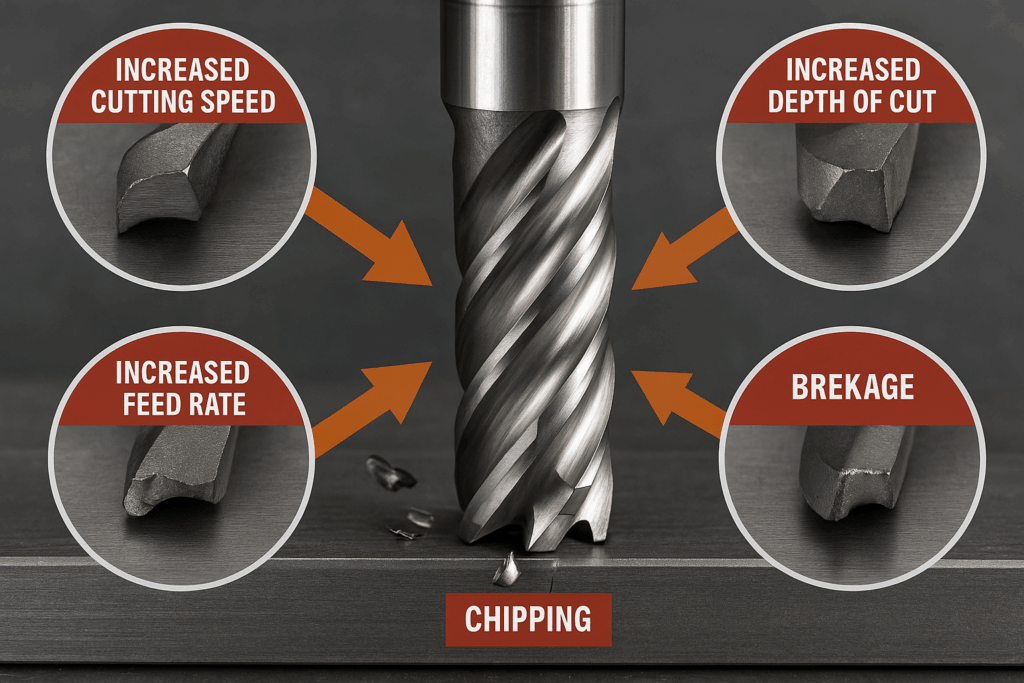
加工現場では、生産性の向上やコスト削減を目的に「切削条件の見直し」が頻繁に行われます。しかし、切削速度・送り速度・切込み量などを変更すると、思わぬ工具損傷や加工トラブルが発生することもあります。本記事では、切削条件の変更によって起こりうる損傷のメカニズムとその対策について解説します。
1. 切削速度(Vc)を上げた場合の影響
切削速度の増加 = 高速加工化は生産性向上のカギですが、同時にリスクも伴います。
主な損傷例:
- 熱摩耗の急激な進行
- 被膜剥離(コーティング工具で発生)
- 高温酸化による工具先端の脆化
対策:
- 高耐熱性コート(TiAlN、AlCrNなど)の採用
- クーラントの適切供給 or ドライ加工への移行検討
2. 送り速度(fz)を増やした場合
送り量の増加は「加工時間の短縮」に直結しますが、工具にかかる負荷が大きくなります。
主な損傷例:
- チッピング(微小欠け)
- 切れ刃の潰れや塑性変形
- 加工面粗さの悪化
対策:
- 強靭性の高い工具材種(超微粒子超硬など)を使用
- 適切なチップブレーカ形状の選定
3. 切込み量(ap, ae)の増加による影響
切込み量を大きくすると、一回あたりの除去体積が増加し、効率は上がります。
主な損傷例:
- 工具全体への過大な負荷
- 工具折損・コーナー破損
- 主軸へのダメージ(びびり誘発)
対策:
- 荒加工では段階的な切込みを設定
- 高剛性なホルダー・工具・工作機械の選定
まとめ
切削条件の変更は、生産性向上の鍵であると同時に、工具損傷の引き金にもなり得ます。加工条件を変更する際は、工具の性能・ワーク材質・機械剛性・冷却方式を総合的に見直すことが重要です。トライアンドエラーだけでなく、加工CAEやシミュレーションツールの活用も効果的です。
このブログを書いた人
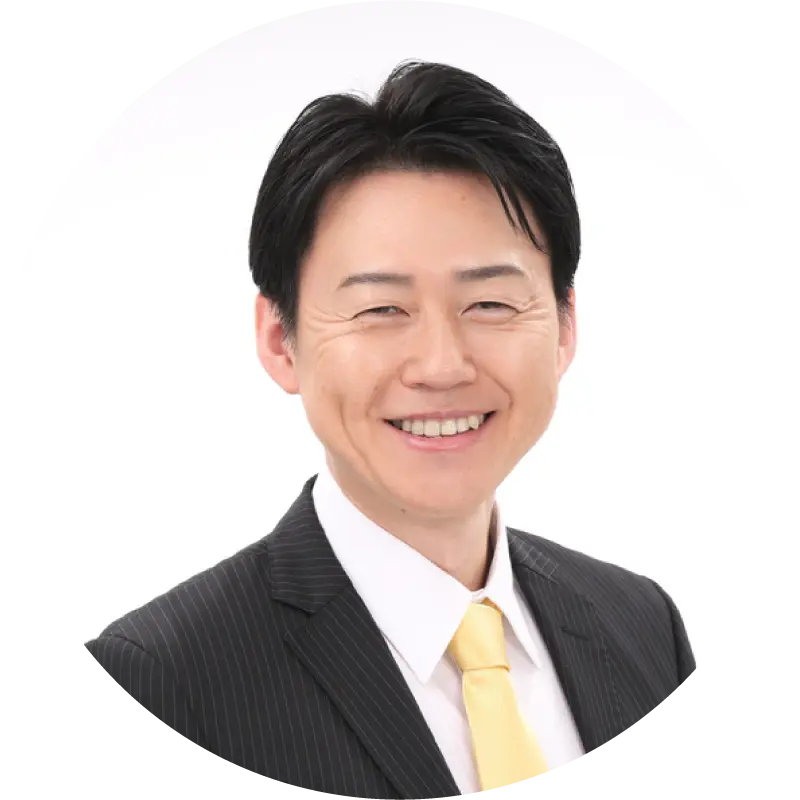
有限会社 長谷川加⼯所
代表取締役
長谷川 一英
HASEGAWA KAZUHIDE
切削加⼯の長谷川加⼯所について
切削加⼯で難しい産業部品を柔軟に製作。
アルミ・スレンレス・鉄 etc。
試作・⼩ロット量産。
詳しくはこちら
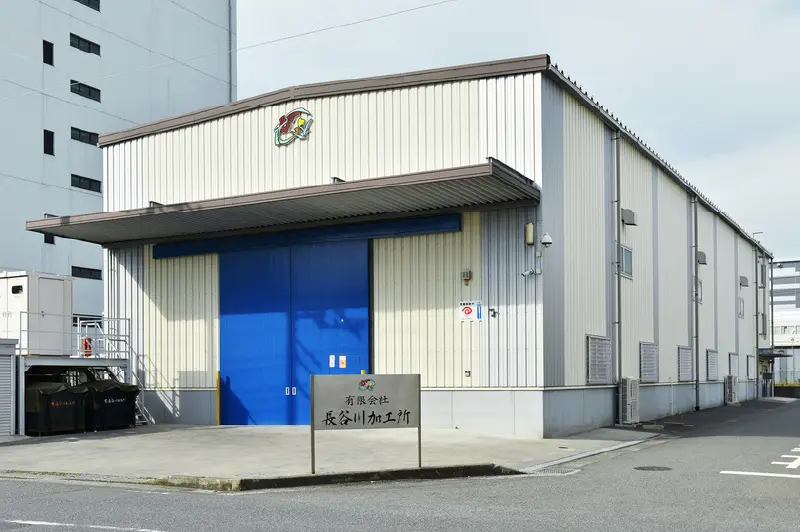