切りくず形態と切削抵抗から学ぶべきこと
カテゴリーblog
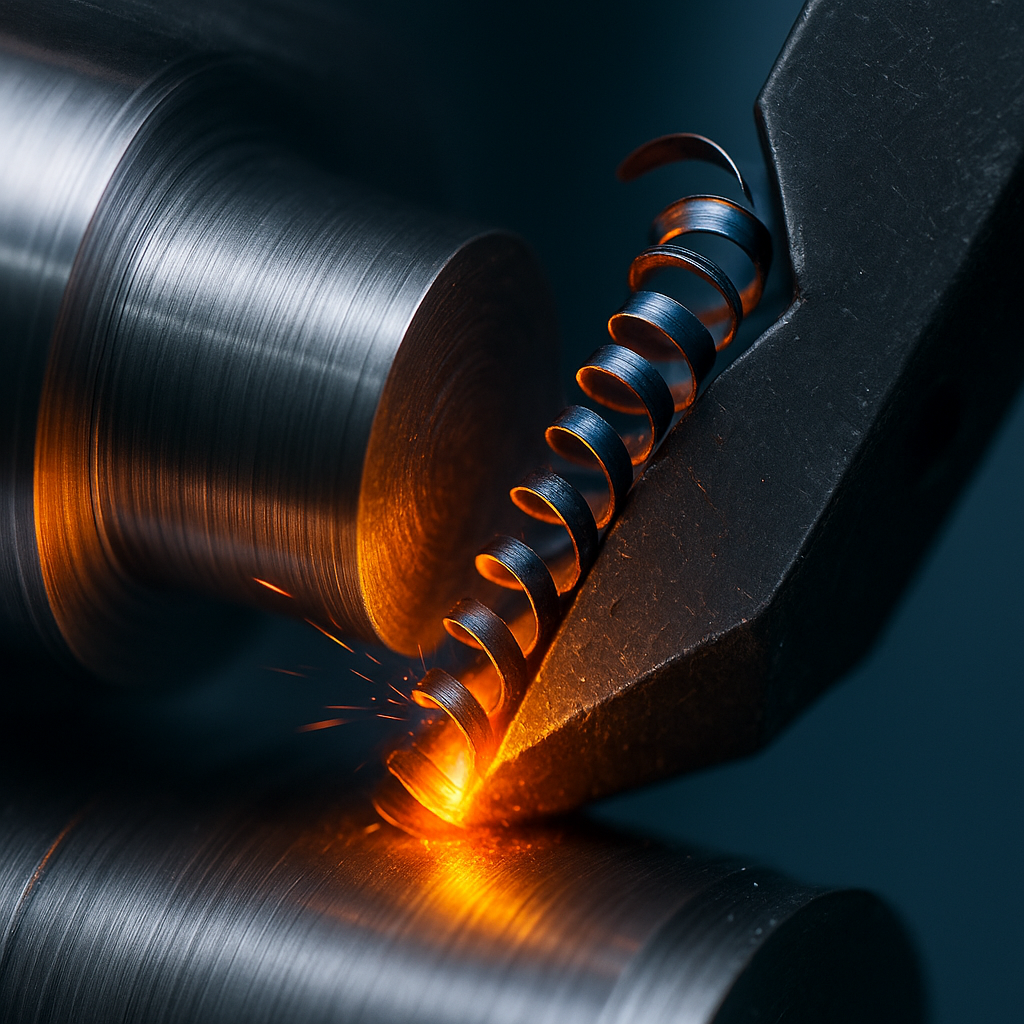
切削加工において「切りくず」は単なる副産物ではなく、加工状態を映す重要な情報源です。特に、切りくずの形態や排出のしやすさは、切削抵抗や工具負荷と密接に関係しており、加工の最適化において見逃せない指標となります。
本記事では、切りくず形態と切削抵抗の関係から見えてくる、加工条件の改善ポイントを解説します。
● 切りくず形態の分類と特徴
- 連続切りくず
→ 滑らかな面を持つリボン状。加工面は美しいが、絡まりや排出不良のリスクあり。 - 断続切りくず
→ 適度な長さで切れている。工具への負荷が少なく、安全性も高い理想的な状態。 - 破砕切りくず
→ 粉砕されたような細片状。加工硬化や高切削抵抗の兆候で、工具摩耗が懸念される。
● 切削抵抗との関係性
切削抵抗が高い場合、以下のような切りくずが発生しやすくなります:
- 厚みがある・硬い切りくず:送り過多や切込み過大、または刃先の摩耗
- 過度に熱変色した切りくず:切削速度が高すぎるか、冷却不足
- 巻き付きや絡まりがある切りくず:逃げ角やチップブレーカ形状の不適合
逆に、切削抵抗が適正であれば、切りくずは自然に排出され、工具寿命や加工品質も安定します。
● 切りくず観察から学ぶべきこと
- 加工条件の再確認
切りくずが長すぎる、変色が激しいなどの兆候があれば、切削条件の見直しを検討。 - 工具の状態確認
切りくずの形が急に変化した場合は、刃先摩耗や欠けの可能性を疑う。 - 被削材の特性把握
同じ条件でも材料のロットや組織によって切りくず性が変化する。
● 改善のためのアプローチ
- チップブレーカ形状の工夫や、切削条件の最適化による切りくず分断
- クーラントの適正使用で熱と摩擦を抑える
- 工具材質やコーティングの選定で刃先の耐久性を確保
切りくずと切削抵抗は、加工の「声」を伝える重要なサインです。目視観察と振動・負荷データの組み合わせで、より高度な加工診断と最適化が可能になります。