臨床データでみる工具寿命低下の主な原因とは?
カテゴリーblog
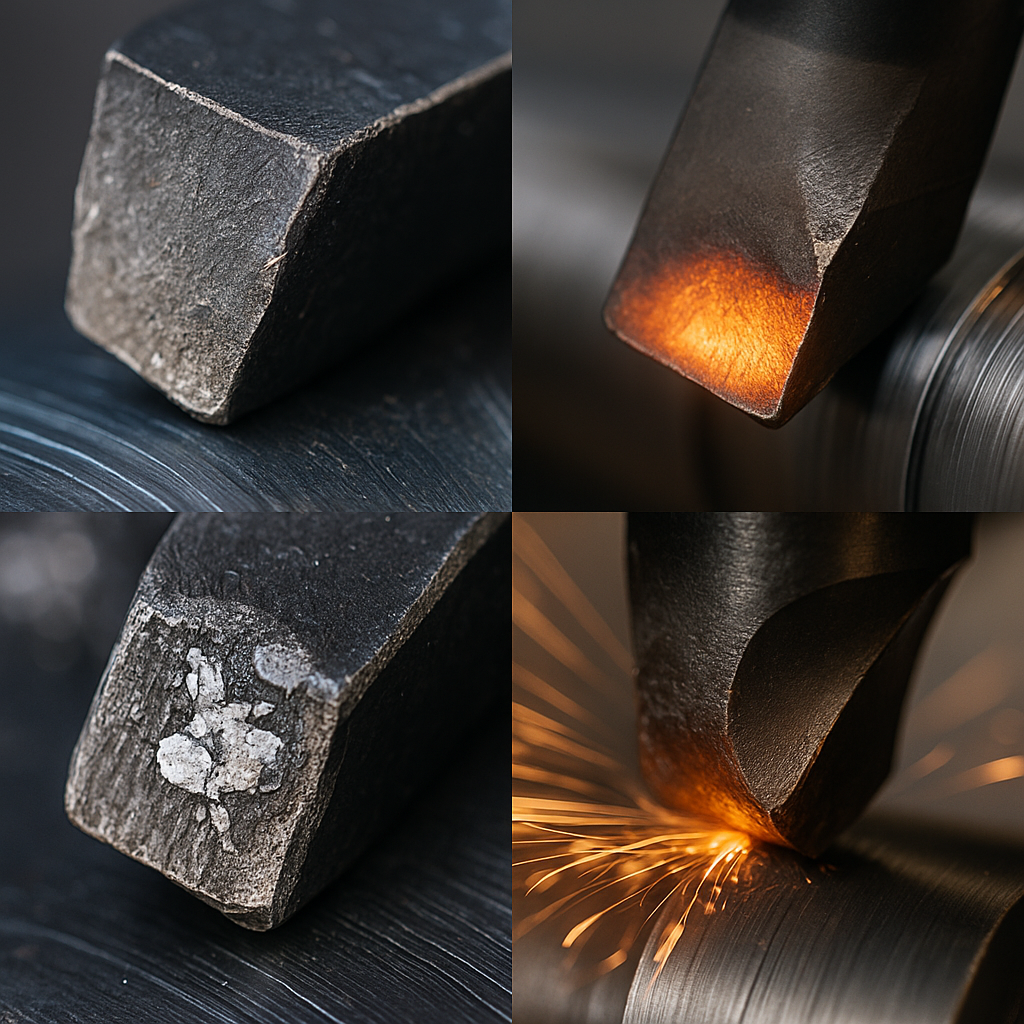
工具の寿命は切削現場の生産性とコストに直結する重要な要素です。現場での「経験」や「勘」も重要ですが、**臨床データ(実加工データ)**に基づいて寿命の原因を分析することで、より客観的・再現性のある改善が可能になります。
本記事では、実際の加工データから読み解いた工具寿命低下の主な原因と、それに対する対応策を紹介します。
● データに基づく寿命低下の主な要因
- 摩耗の進行(フランク摩耗・クレータ摩耗)
→ 加工時間や送り速度に比例して摩耗が進行。特に高硬度材や高切削速度下では寿命を大幅に縮める。 - チッピング・欠損
→ 加工条件の急変(断続切削・過大な切込みなど)により刃先が微細に破損し、予期せぬ工具破損が起こる。 - 溶着と刃先形状変化
→ 親和性の高い材料(ステンレス、アルミなど)を無潤滑で加工した際に発生しやすく、切れ味を低下させる。 - 熱変質によるコーティング剥離
→ 高温域での連続加工によりコーティングの劣化が進み、ベース材の露出とともに摩耗加速。 - 機械振動(びびり)
→ 工具・ワーク剛性やクランプ不良が原因。振動によって工具の局所的な負荷が増加し、寿命を短縮。
● 対応策とデータの活用方法
- 切削条件の適正化
→ 加工データ(切削力・温度・音・振動)をモニタリングし、適正条件を導出。 - ツールマネジメントシステムの導入
→ 工具ごとの寿命・摩耗履歴を一元管理し、交換タイミングを最適化。 - コーティング・工具材質の見直し
→ 被削材に対する親和性や耐熱性を考慮して選定。 - 試験加工データの蓄積と活用
→ 少量試作段階からのデータを蓄積し、本番加工へのフィードバックを行う。
臨床データに基づいた工具寿命の管理は、属人的な判断からの脱却と生産性の向上につながります。加工トラブルを未然に防ぐためにも、「使った結果」から「次に活かす」仕組みづくりが求められます。