旋削加工の諸特性を学ぼう!|切削現象から工具選定までの基本を解説
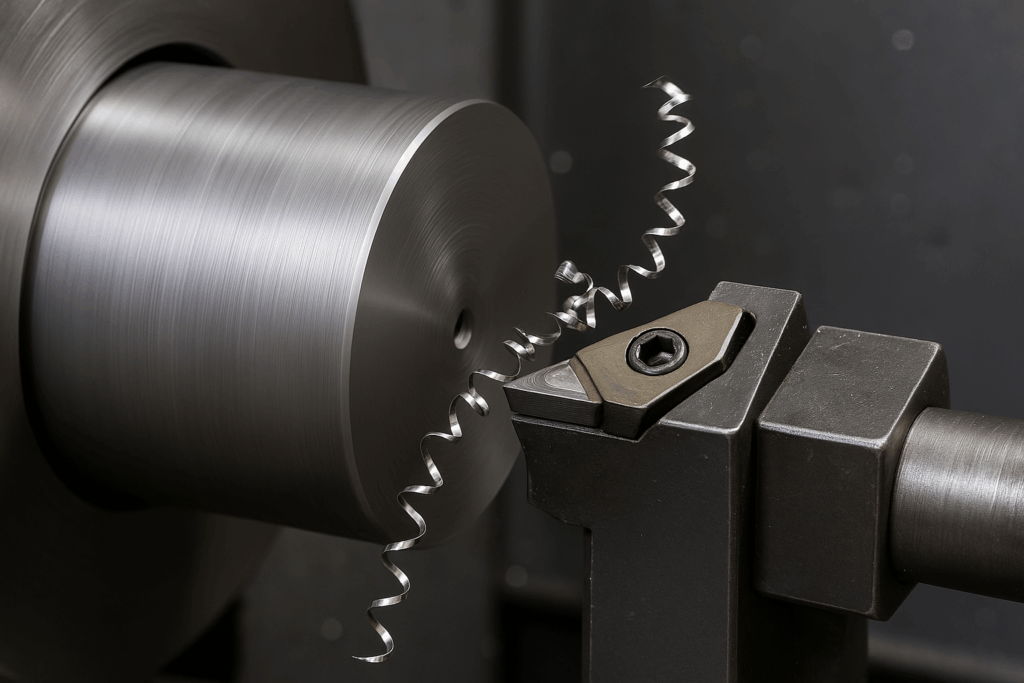
旋削加工(ターニング)は、工作物を回転させて、固定された切削工具で材料を除去する加工方法です。旋盤を用いたこの基本的な加工法は、円筒形状やねじ切り、内径加工など、幅広い形状に対応できる汎用性の高い技術です。本記事では、旋削加工における代表的な特性について解説します。
1. 切削力と加工精度
旋削加工では、切削工具がワークに接触する際に主切削力・送り力・背分力の3成分が発生します。特に主切削力は工具摩耗や仕上がり精度に直結するため、最適な切削条件(切削速度・送り量・切込み深さ)を選定することが重要です。
2. 工具寿命と摩耗形態
旋削加工でもっとも多く使われるのがチップ式工具(インサート)。工具の摩耗にはクレータ摩耗、フランク摩耗、ノッチ摩耗などがあり、被削材や切削条件により進行の仕方が異なります。特に硬度の高い材料では、耐摩耗性に優れたコーティング工具が有効です。
3. 切りくずの形態
旋削加工では連続切りくずが発生しやすく、切りくずの巻き付きや排出不良がトラブルの原因となります。チップブレーカ付き工具や切削油の使用によって、切りくず制御を図ることが推奨されます。
4. 表面粗さと加工面品質
加工後の表面粗さは、主に送り量に依存します。仕上げ加工では低送り・小切込みで工具を走らせることで、高い面粗さ精度(低Ra値)を達成できます。また、刃先のホーニング状態や工具材質も仕上がりに影響を及ぼします。
5. 適正な工具選定
被削材の材質(炭素鋼・ステンレス鋼・鋳鉄など)や用途(荒加工・仕上げ加工)に応じて、適正なチップ材種、形状、コーティングを選定することが、生産性・工具寿命の両立に繋がります。
■ まとめ
旋削加工は、基本でありながら奥の深い切削法です。加工トラブルを回避し、高品質な製品を安定的に生み出すには、諸特性の理解と適切な工具・条件の設定が不可欠です。今一度、旋削加工の基礎を見直してみましょう。