ステンレス鋼と耐熱鋼を削る!一般的推奨切削条件まとめ
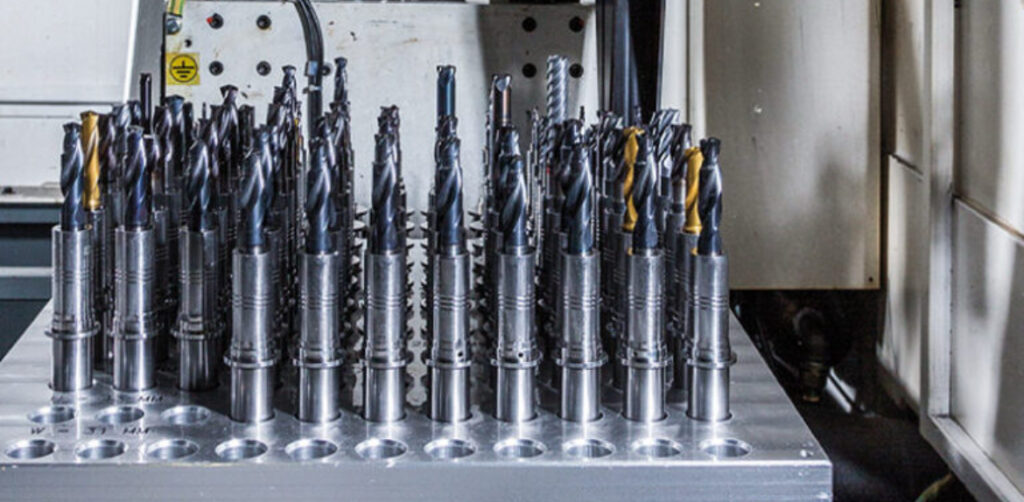
はじめに
ステンレス鋼や耐熱鋼は、耐食性や耐熱性に優れる一方で、切削加工が難しい「難削材」として知られています。特に加工硬化のしやすさや熱のこもりやすさ、切りくず処理の難しさなどが工具寿命や加工品質に大きな影響を与えます。本記事では、それぞれの材料特性に応じた一般的な推奨切削条件をご紹介します。
ステンレス鋼の加工ポイント
オーステナイト系(SUS304、SUS316など)のステンレス鋼は、熱伝導率が低く、加工中の熱が刃先に集中しやすいため、工具摩耗が早く進みます。また、加工硬化が起こりやすいため、浅い切込みや再切削は避けるべきです。
切削速度は超硬工具を用いた場合でおおよそ40~80m/minが目安です。高速度鋼工具ではさらに低く、15~25m/min程度に抑える必要があります。送り量は仕上げ加工で0.05~0.2mm/revが一般的です。切込み深さは0.5~3mm程度を目安とし、しっかり一発で削る意識が重要です。
また、ステンレス鋼では溶着によるトラブルも多いため、クーラントは高圧で確実に供給し、刃先の冷却と切りくず排出を促すことが求められます。工具にはTiAlNやAlCrNなどの耐熱コーティング付き超硬製品が有効です。
耐熱鋼の加工ポイント
インコネル(Inconel)やハステロイ(Hastelloy)、ワスパロイ(Waspaloy)などの耐熱合金は、非常に高い強度と耐熱性を持つ一方で、工具にとっては過酷な条件です。加工中は高温状態が持続し、摩耗やチッピングが起こりやすいため、切削速度は20~40m/minとかなり低速に設定する必要があります。
送り量は0.02~0.15mm/revが目安で、過大な負荷がかからないように注意します。切込みは0.3~2mm程度と控えめに。高硬度で加工硬化も起きやすいため、切込みは1回で確実に仕上げるのが理想です。
使用する工具は、耐摩耗性と耐熱性に優れたCBNインサートや、ナノ多層コーティングを施した超硬工具が適しています。クーラントは内部給油による高圧供給が前提で、切削点への確実な到達が求められます。
加工トラブルを防ぐコツ
ビビリの防止には、工具の突き出し長さを最小限に抑えることが有効です。また、切りくず排出がうまくいかないと摩耗が加速するため、切れ刃形状にも注目する必要があります。
再切削や空切りは加工硬化を進行させ、刃先破損の原因になるため、切削条件は常に「一発勝負」で設定しましょう。
おわりに
ステンレス鋼と耐熱鋼の切削では、材料特性に応じた切削速度、送り、切込み、工具材質の選定が不可欠です。また、適切なクーラント供給や工具管理も不可欠な要素です。正しい条件設定と工具選びによって、加工トラブルを回避し、安定した高品質加工が実現できます。
このブログを書いた人
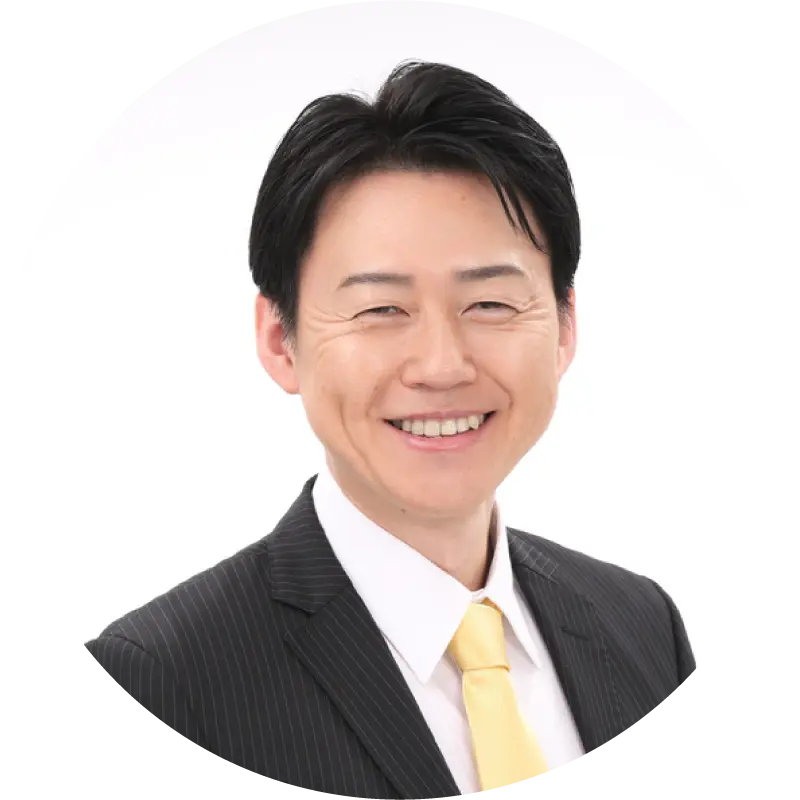
有限会社 長谷川加⼯所
代表取締役
長谷川 一英
HASEGAWA KAZUHIDE
切削加⼯の長谷川加⼯所について
切削加⼯で難しい産業部品を柔軟に製作。
アルミ・スレンレス・鉄 etc。
試作・⼩ロット量産。
詳しくはこちら
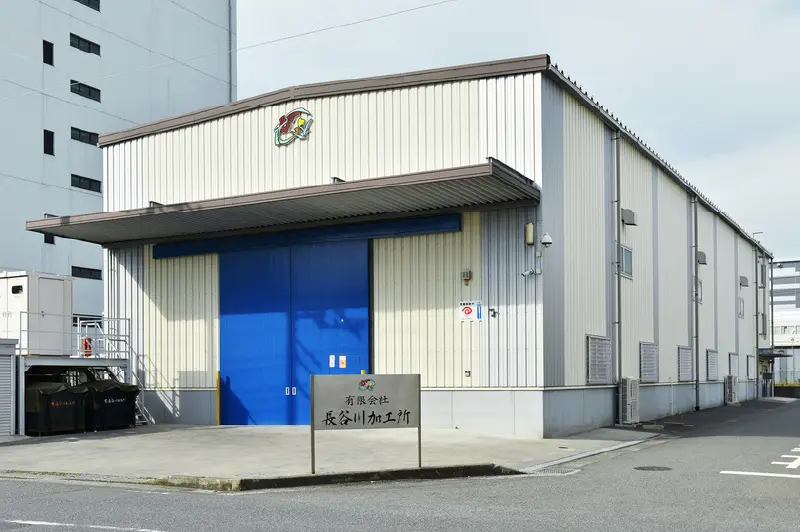